Why Do Mechanical Engineers Hate Designing Products?
Why Do Mechanical Engineers Hate Designing Products?
Why Do Mechanical Engineers Hate Designing Products?
Dr. Maor Farid, Co-Founder & CEO at Leo AI
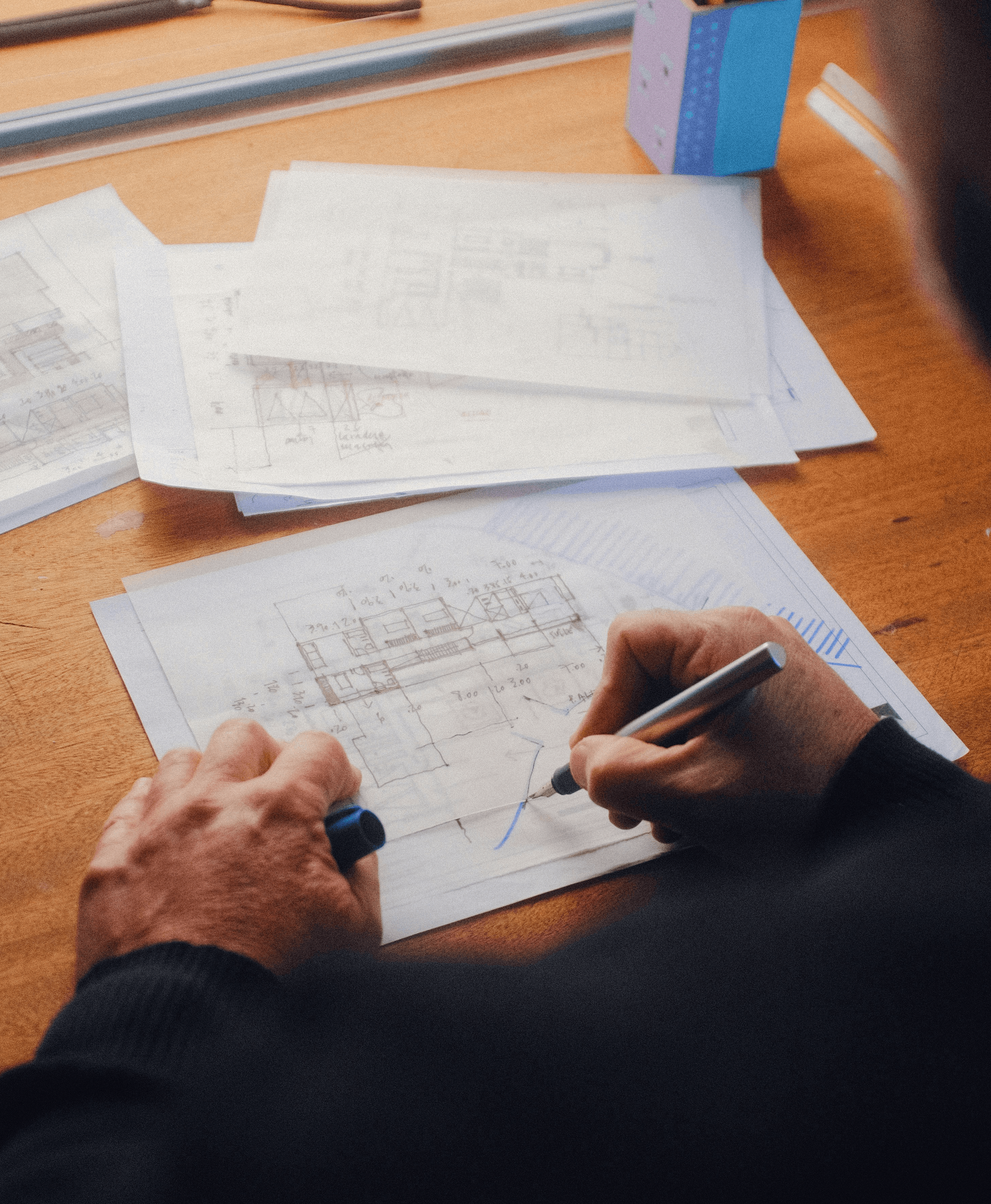
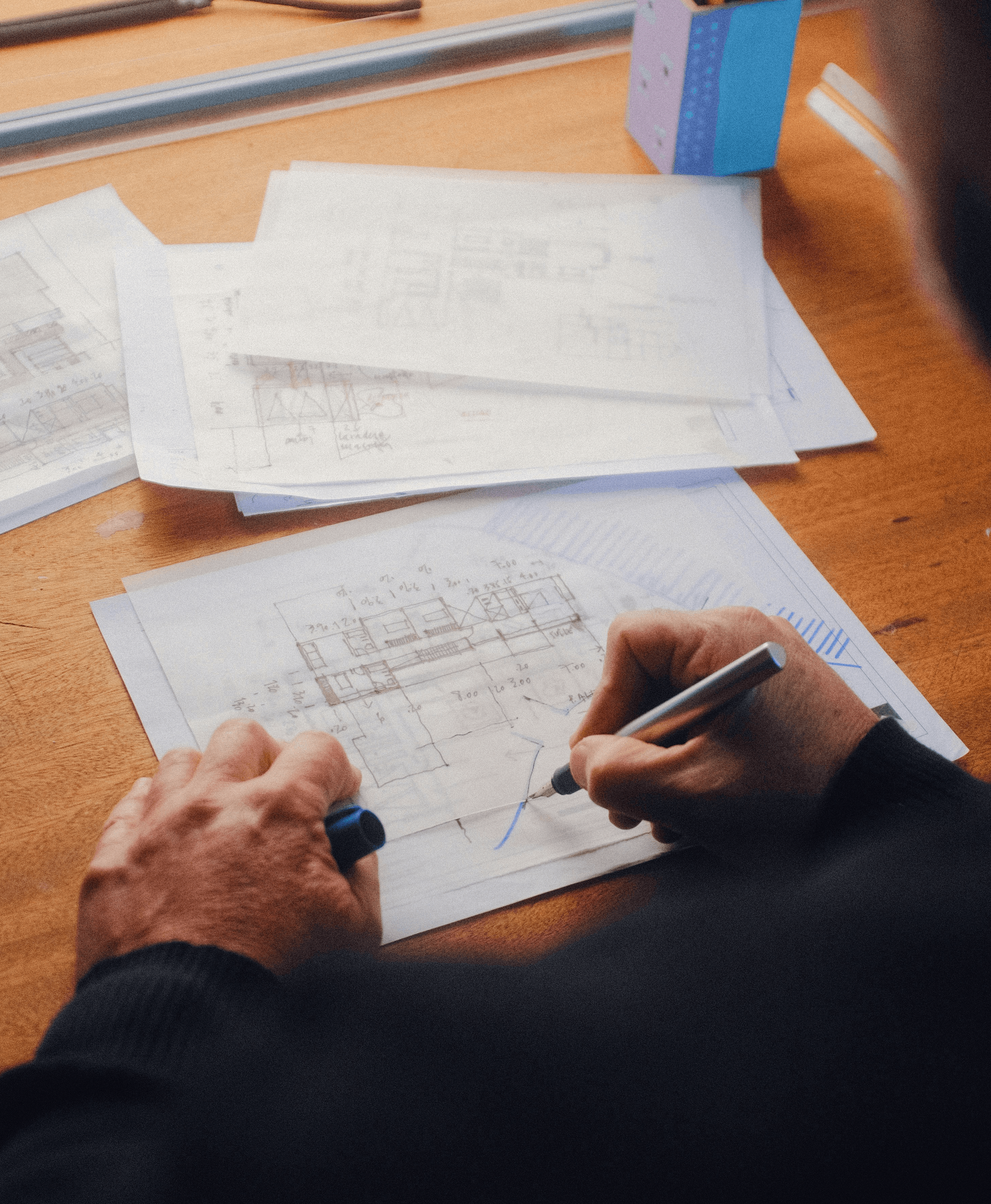
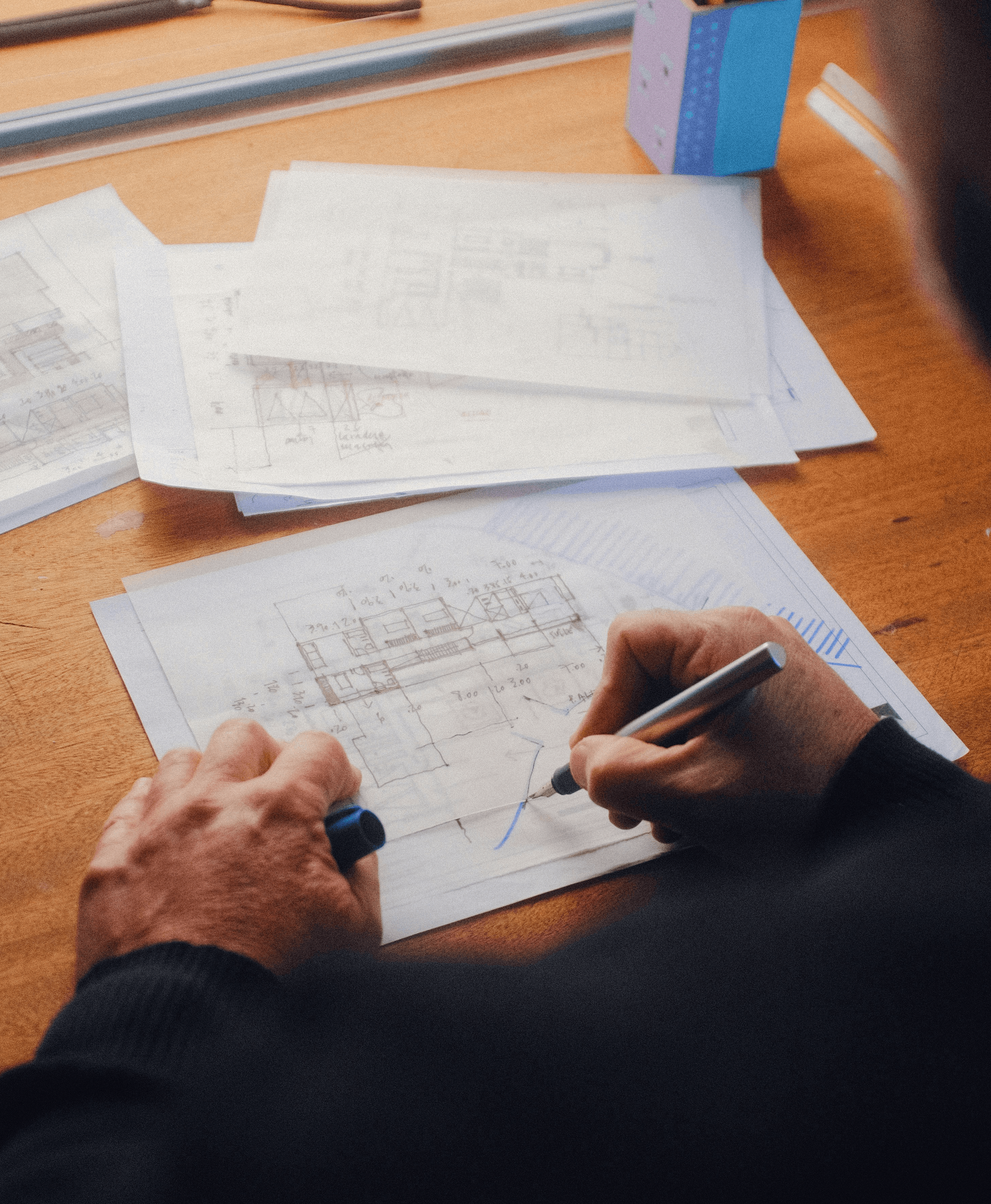
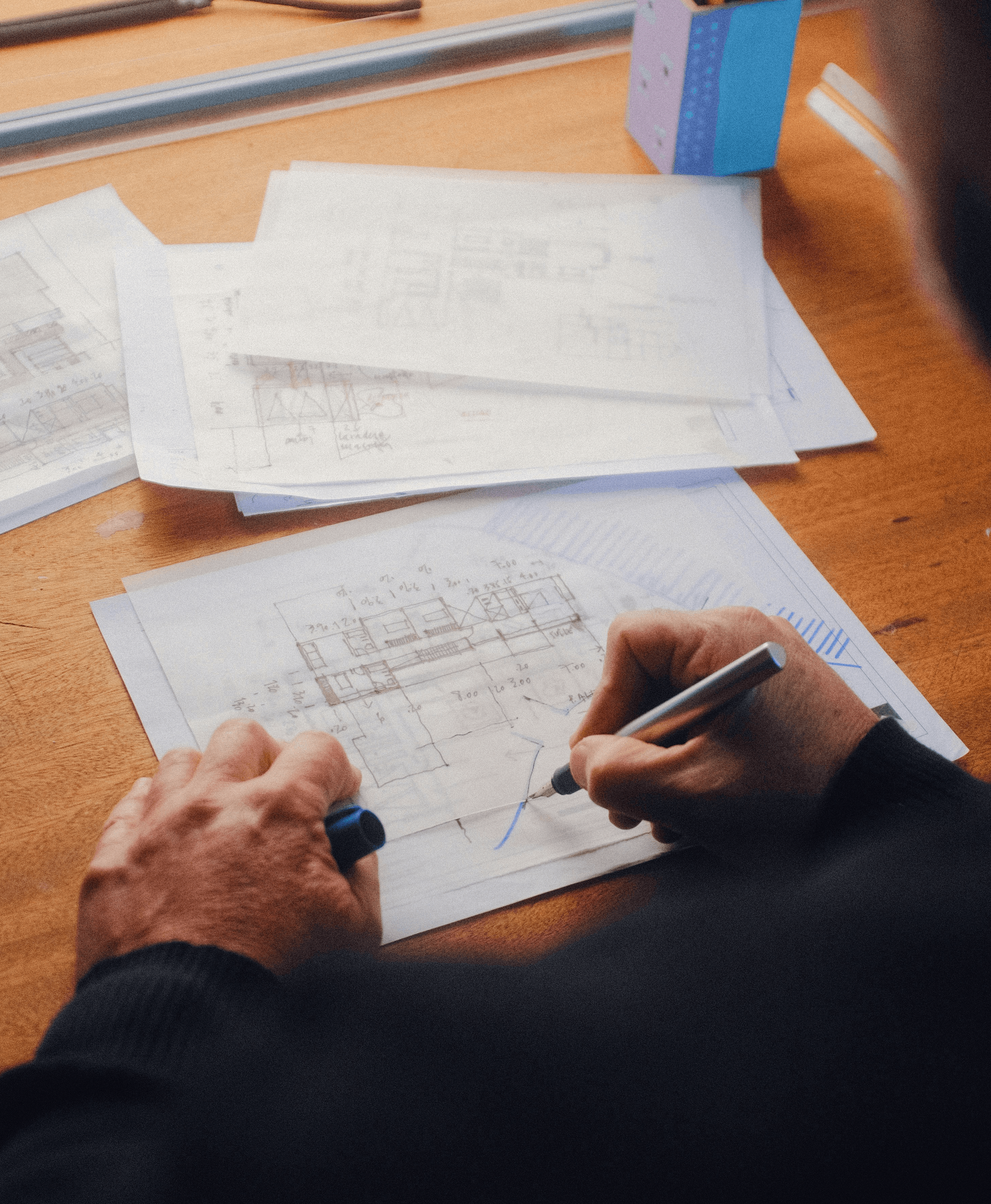
Mechanical engineering is often celebrated as a field of boundless innovation, where creative minds transform ideas into tangible realities. However, behind the scenes, the process of designing products is fraught with frustration, inefficiency, and fragmentation. Despite the allure of engineering marvels, many mechanical engineers find themselves grappling with a system that feels more like a relic of the past than a gateway to the future.
The Cumbersome, Fragmented Process of Product Design
In today's market, over $100 billion is spent annually on software and labor for hardware design and data management. Companies are willing to pay hefty sums—ranging from $5,000 to $12,000 per seat per year for CAD tools, plus an additional $20,000 per year for PLM costs. Salaries for full-time personnel to manage these systems further inflate these expenses. Yet, despite these investments, the tools and processes engineers rely on remain deeply flawed.
"In today's market, over $100 billion is spent annually on software and labor for hardware design and data management." (Niazi et al., 2006)
The current design process, from requirements to assembly, is fragmented across various tools:
Requirements: Managed in Confluence
Design: Created in SolidWorks
Simulations: Conducted in Ansys
Procurement: Handled through emails and platforms like Xometry
Manufacturing: Documented in PDFs, CAD files, and PowerPoints
Assembly: Executed manually
Each stage relies on discrete tools, leading to inefficiencies and errors. Engineers often find themselves buried in versions of documents, struggling with complicated naming conventions, and dealing with notification fatigue. This disjointed system results in significant delays and miscommunication.
The Daily Struggles of Mechanical Engineers
Mechanical engineers spend a staggering 12 hours a week searching for models and even longer redesigning existing ones. This is not just a minor inconvenience—it significantly hampers productivity and innovation. As one engineer put it, "I spend a lot of time implementing shapes and structures instead of actually engineering" [1].
The process of designing, editing, and collaborating is equally tedious. Engineers check in and out CAD files from the PLM system, making modifications, and saving updates. Managers then review and approve these designs, often resulting in a back-and-forth exchange of emails, phone calls, and screen-sharing sessions. This not only consumes time but also increases the risk of errors and miscommunication.
"Engineers often find themselves buried in versions of documents, struggling with complicated naming conventions, and dealing with notification fatigue." [2]
Moreover, the existing PLM and CAD tools have their own sets of problems:
PLM Issues: Low NPS, multiple versions of documents, lack of automatic updates, limited to one editor at a time, and high noise-to-signal ratio in notifications [2].
CAD Tool Issues: Trade-offs between usability and performance, reliance on multiple tools for different tasks, minimal integration, and repetitive work [3].
The current system for design for manufacturing and vendor review is equally cumbersome. Engineers and managers must coordinate with external stakeholders through emails, phone calls, and text feedback, leading to further delays and inefficiencies. This fragmented process is documented in systems like SolidWorks PDM but lacks cohesion and fluidity.
The Opportunity in the GenAI Era
Enter the era of Generative AI, which presents an unprecedented opportunity to rethink and revolutionize the entire product design process. By harnessing the power of advanced algorithms and machine learning, Generative AI can streamline the transition from requirements to assembly, eliminating many of the pain points that plague the current system.
Generative AI has the potential to integrate and automate various stages of the design process, offering a unified platform that can handle requirements, design, simulations, procurement, and manufacturing seamlessly. This not only reduces the time and effort required but also enhances accuracy and innovation [4].
"Generative AI has the potential to integrate and automate various stages of the design process, offering a unified platform that can handle requirements, design, simulations, procurement, and manufacturing seamlessly."
Imagine a world where mechanical engineers can articulate their design visions, and an AI-powered system generates editable technical specifications, conceptual illustrations, and fully detailed CAD assemblies in real-time. This is not a distant dream but a tangible reality that Generative AI promises to deliver [5].
Conclusion
Mechanical engineers have long endured the frustrations of a cumbersome and fragmented product design process. However, with the advent of Generative AI, there is hope on the horizon. By embracing this cutting-edge technology, we can streamline workflows, accelerate innovation, and unlock new possibilities that were previously unimaginable. It's time to revolutionize the field of mechanical engineering and product design, empowering engineers to focus on what they do best—innovate and create.
References
Niazi, A., Dai, J.S., Balabani, S. & Seneviratne, L. (2006). Cost estimation in product development: Academic research and commercial systems. Journal of Engineering Design, 17, 143-164.
Engineering.com. (2020). The Challenges of PLM in Mechanical Engineering. Engineering.com. Retrieved from https://www.engineering.com/story/the-challenges-of-plm-in-mechanical-engineering
Onshape. (2021). Survey on Time Spent by Engineers on Data Management. Onshape. Retrieved from https://www.onshape.com/en/resource-center/white-papers/survey-on-time-spent-by-engineers-on-data-management
Chaudhuri, A., Koltun, V. & Funkhouser, T. (2020). Generative design: An exploration of the state of the art and future directions. Computer-Aided Design, 123, 102-115.
Autodesk. (2019). Generative Design in Aerospace: Airbus Case Study. Autodesk. Retrieved from https://www.autodesk.com/customer-stories/airbus
Leo AI 160 Alewife Brook Pkwy #1095, Cambridge, MA 02138, USA
Mechanical engineering is often celebrated as a field of boundless innovation, where creative minds transform ideas into tangible realities. However, behind the scenes, the process of designing products is fraught with frustration, inefficiency, and fragmentation. Despite the allure of engineering marvels, many mechanical engineers find themselves grappling with a system that feels more like a relic of the past than a gateway to the future.
The Cumbersome, Fragmented Process of Product Design
In today's market, over $100 billion is spent annually on software and labor for hardware design and data management. Companies are willing to pay hefty sums—ranging from $5,000 to $12,000 per seat per year for CAD tools, plus an additional $20,000 per year for PLM costs. Salaries for full-time personnel to manage these systems further inflate these expenses. Yet, despite these investments, the tools and processes engineers rely on remain deeply flawed.
"In today's market, over $100 billion is spent annually on software and labor for hardware design and data management." (Niazi et al., 2006)
The current design process, from requirements to assembly, is fragmented across various tools:
Requirements: Managed in Confluence
Design: Created in SolidWorks
Simulations: Conducted in Ansys
Procurement: Handled through emails and platforms like Xometry
Manufacturing: Documented in PDFs, CAD files, and PowerPoints
Assembly: Executed manually
Each stage relies on discrete tools, leading to inefficiencies and errors. Engineers often find themselves buried in versions of documents, struggling with complicated naming conventions, and dealing with notification fatigue. This disjointed system results in significant delays and miscommunication.
The Daily Struggles of Mechanical Engineers
Mechanical engineers spend a staggering 12 hours a week searching for models and even longer redesigning existing ones. This is not just a minor inconvenience—it significantly hampers productivity and innovation. As one engineer put it, "I spend a lot of time implementing shapes and structures instead of actually engineering" [1].
The process of designing, editing, and collaborating is equally tedious. Engineers check in and out CAD files from the PLM system, making modifications, and saving updates. Managers then review and approve these designs, often resulting in a back-and-forth exchange of emails, phone calls, and screen-sharing sessions. This not only consumes time but also increases the risk of errors and miscommunication.
"Engineers often find themselves buried in versions of documents, struggling with complicated naming conventions, and dealing with notification fatigue." [2]
Moreover, the existing PLM and CAD tools have their own sets of problems:
PLM Issues: Low NPS, multiple versions of documents, lack of automatic updates, limited to one editor at a time, and high noise-to-signal ratio in notifications [2].
CAD Tool Issues: Trade-offs between usability and performance, reliance on multiple tools for different tasks, minimal integration, and repetitive work [3].
The current system for design for manufacturing and vendor review is equally cumbersome. Engineers and managers must coordinate with external stakeholders through emails, phone calls, and text feedback, leading to further delays and inefficiencies. This fragmented process is documented in systems like SolidWorks PDM but lacks cohesion and fluidity.
The Opportunity in the GenAI Era
Enter the era of Generative AI, which presents an unprecedented opportunity to rethink and revolutionize the entire product design process. By harnessing the power of advanced algorithms and machine learning, Generative AI can streamline the transition from requirements to assembly, eliminating many of the pain points that plague the current system.
Generative AI has the potential to integrate and automate various stages of the design process, offering a unified platform that can handle requirements, design, simulations, procurement, and manufacturing seamlessly. This not only reduces the time and effort required but also enhances accuracy and innovation [4].
"Generative AI has the potential to integrate and automate various stages of the design process, offering a unified platform that can handle requirements, design, simulations, procurement, and manufacturing seamlessly."
Imagine a world where mechanical engineers can articulate their design visions, and an AI-powered system generates editable technical specifications, conceptual illustrations, and fully detailed CAD assemblies in real-time. This is not a distant dream but a tangible reality that Generative AI promises to deliver [5].
Conclusion
Mechanical engineers have long endured the frustrations of a cumbersome and fragmented product design process. However, with the advent of Generative AI, there is hope on the horizon. By embracing this cutting-edge technology, we can streamline workflows, accelerate innovation, and unlock new possibilities that were previously unimaginable. It's time to revolutionize the field of mechanical engineering and product design, empowering engineers to focus on what they do best—innovate and create.
References
Niazi, A., Dai, J.S., Balabani, S. & Seneviratne, L. (2006). Cost estimation in product development: Academic research and commercial systems. Journal of Engineering Design, 17, 143-164.
Engineering.com. (2020). The Challenges of PLM in Mechanical Engineering. Engineering.com. Retrieved from https://www.engineering.com/story/the-challenges-of-plm-in-mechanical-engineering
Onshape. (2021). Survey on Time Spent by Engineers on Data Management. Onshape. Retrieved from https://www.onshape.com/en/resource-center/white-papers/survey-on-time-spent-by-engineers-on-data-management
Chaudhuri, A., Koltun, V. & Funkhouser, T. (2020). Generative design: An exploration of the state of the art and future directions. Computer-Aided Design, 123, 102-115.
Autodesk. (2019). Generative Design in Aerospace: Airbus Case Study. Autodesk. Retrieved from https://www.autodesk.com/customer-stories/airbus